The Essential Guide to Press Brakes in Sheet Metal Fabrication
In the world of sheet metal fabrication, precision and efficiency are paramount. Among the many tools available to achieve these goals, the press brake stands out as an indispensable asset. Whether you’re a seasoned fabricator or a novice exploring the industry, understanding the role and capabilities of a press brake is crucial. This guide will delve into the essentials of press brakes, their significance in sheet metal fabrication, and how they can elevate your manufacturing processes.
What is a Press Brake?
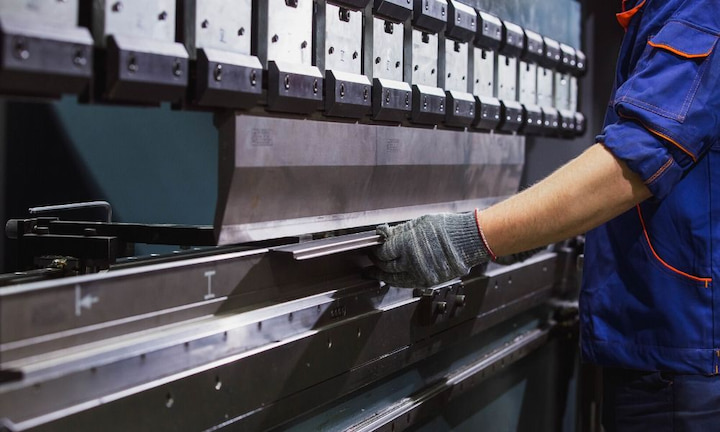
A press brake is a machine used to bend sheet metal into various shapes and angles. It operates by clamping the metal between a matching punch and die, then applying force to bend the metal to the desired angle. The press brake can perform a wide range of bends, making it versatile for creating complex parts and components.
Types of Press Brakes
There are several types of press brakes, each suited to different applications and production needs. The most common types include:
- Mechanical Press Brakes: These utilize a flywheel powered by an electric motor to generate force. Known for their speed and precision, mechanical press brakes are suitable for high-volume production.
- Hydraulic Press Brakes: Using hydraulic cylinders to apply pressure, these machines offer greater flexibility and control over the bending process. They are ideal for handling thick or tough materials and are often used in heavy-duty applications.
- CNC Press Brakes: Computer Numerical Control (CNC) press brakes are equipped with automated controls for precise bending. They are highly versatile and can perform complex bends with minimal manual intervention, making them perfect for intricate designs and high-precision work.
- Pneumatic Press Brakes: Powered by compressed air, these are generally used for lighter materials and less demanding tasks. They are cost-effective and easy to operate but lack the power of hydraulic and mechanical press brakes.
Key Components of a Press Brake
Understanding the key components of a press brake helps in appreciating its functionality:
- Bed: The flat surface where the sheet metal is placed.
- Ram: The moving component that presses the punch into the die to bend the metal.
- Punch: The tool attached to the ram, which forms the upper part of the bend.
- Die: The lower tool that works in conjunction with the punch to shape the metal.
- Backgauge: A device that positions the metal accurately for each bend.
- Control System: In CNC press brakes, this system controls the machine’s operations and ensures precision.
Advantages of Using a Press Brake
1. Precision and Accuracy
Press brakes are designed to produce precise bends with tight tolerances. The use of CNC technology further enhances accuracy, allowing for repeatable and consistent results. This precision is critical in industries where exact specifications are mandatory, such as aerospace and automotive manufacturing.
2. Versatility
With the ability to perform a wide range of bends and accommodate various materials, press brakes are incredibly versatile. They can handle different sheet thicknesses and types of metals, from aluminium to stainless steel, making them suitable for diverse applications.
3. Efficiency
Press brakes streamline the bending process, reducing the time and effort required to shape metal parts. CNC press brakes, in particular, offer automated functions that minimize manual intervention and speed up production cycles. This efficiency translates to increased productivity and reduced labour costs.
4. Customization
Press brakes allow for significant customization in metal fabrication. Operators can adjust the angle, depth, and radius of bends to create bespoke components tailored to specific requirements. This capability is invaluable in custom fabrication projects.
Applications of Press Brakes
Press brakes are used across various industries for different applications, including:
- Automotive: Fabricating parts like brackets, frames, and panels.
- Aerospace: Producing components that require high precision and durability.
- Construction: Creating structural elements, roofing, and cladding.
- Electronics: Manufacturing enclosures, chassis, and other housing components.
- Furniture: Crafting metal parts for office and home furniture.
Factors to Consider When Choosing a Press Brake
Selecting the right press brake involves considering several factors to ensure it meets your fabrication needs:
- Material Type and Thickness: Determine the types of metals and their thicknesses that you will be working with. This will influence the tonnage and capacity required.
- Bend Length and Depth: Consider the maximum length and depth of bends you need to perform. This will dictate the size and type of press brake suitable for your operations.
- Production Volume: Assess your production requirements. For high-volume production, a mechanical or CNC press brake may be more suitable due to its speed and automation capabilities.
- Precision Requirements: For applications that demand high precision, a CNC press brake is the best choice due to its advanced control systems.
- Budget: Balance your budget against the features and capabilities you need. While CNC press brakes are more expensive, they offer superior precision and efficiency that can justify the investment in the long run.
Maintenance and Safety

Regular maintenance of a press brake is crucial to ensure its longevity and optimal performance. Key maintenance tasks include:
- Lubrication: Regularly lubricate moving parts to prevent wear and tear.
- Inspection: Conduct routine inspections for any signs of damage or wear, particularly on the punch and die.
- Calibration: Ensure the machine is properly calibrated to maintain precision.
- Cleanliness: Keep the machine clean and free of debris to avoid operational issues.
Safety is also paramount when operating a press brake. Operators should be trained to handle the machine safely and follow all safety protocols, including using protective gear and ensuring the work area is free of hazards.
Conclusion
In sheet metal fabrication, the press brake is a cornerstone tool, offering unparalleled precision, versatility, and efficiency. Whether you’re fabricating automotive parts, aerospace components, or custom metal projects, a press brake can significantly enhance your capabilities and output. By understanding the different types of press brakes, their components, and their benefits, you can make an informed decision to choose the right machine for your needs. Investing in a high-quality press brake not only improves your production process but also ensures that you can meet the demanding requirements of modern fabrication with confidence and ease.