The Best Tips on How to Extend the Life of Your Pottery Kiln
When artists and artistically-minded people buy a new kiln, they’re so excited that they don’t think much about its maintenance. However, kilns wear out – faster if you use them more. Just like cars, they require replacing their worn-out parts. And just like a car, your pottery kiln will function better and survive longer if you regularly maintain it.
Sometimes tedious and often inconvenient, regular maintenance isn’t as exciting as creating art. It takes time and effort, but the benefits—longer element life, better firings, and fewer breakdowns—far outweigh it.
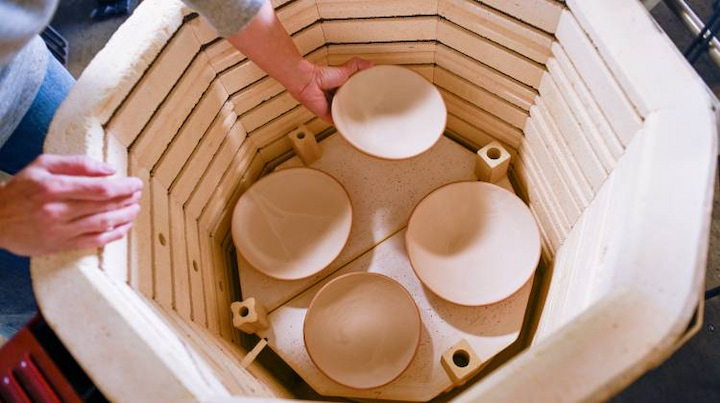
How Do You Maintain a Kiln?
Once you’ve chosen the correct kiln for the job, you must regularly do specific checkups regarding its temperature, elements and level of cleanliness. Pyrometric cones, kiln props, adhesives and wash, and the correct replacement props are some of the ceramics kiln essentials that’ll make the maintenance process a lot easier for you.
Maintaining Kiln Temperature
Temperature control is crucial since working at high temperatures can be dangerous. If you wish consistent results with every firing, you must check the temperature within your kiln.
While underheating will prevent the clay from vitrifying and the glaze from melting properly, overfiring can harm your product. Thus, monitoring the temperature in your ceramic kiln is crucial. Most modern kilns are thermocouple-operated unless you have a sitter or run yours manually using pyrometric cones.
Thermocouple Maintenance
Amazingly, the thermocouple probe uses magnetism and electricity to measure the temperature inside your kiln. Successful firing depends on the thermocouple receiving routine maintenance. It’s necessary to examine the thermocouple for indications of damage.
Carrying an additional thermocouple with you can be very beneficial; if there are any problems, you can replace them immediately. Pyrometric cones are a helpful tool for checking the accuracy of thermocouples to ensure proper operation. Using pyrometric cones is something experts advise doing at least every second firing if your kiln is older.
Use three cones with varying temperature ranges to get better results. For example, you can use cones 4, 5, and 6 if you fire cone 5. When the temperature rises, cone no. 4 will melt and flex. At the appropriate temperature, cone no. 5 will bend halfway. Furthermore, when the temperature drops below the necessary level, cone no. 6 won’t bend. Put them up against the spyhole so you can use safety glasses to peek at them.
Kiln Sitter Maintenance
For ceramics kilns with manual controls, a kiln sitter is an essential part. This gadget automatically shuts off upon reaching the intended firing temperature. You must incorporate proper cleaning and adjustment of the sitter into your monthly maintenance. The small pyrometric cone supports the sensing rod, which has to be able to cut the kiln off when the witness cone bends.
Inspecting the sitters is paramount to maintain them in maximum operating order, as malfunctioning ones might result in overfired or underfired ceramics. Consider investing in digital controllers since these can help you monitor temperatures more precisely than the manual alternative.
Kiln Vents
The ideal room temperature is crucial to a successful fire. Ensure you keep the environment cold and well-ventilated. Get a vent system or place your kiln in an area with good ventilation. A vent keeps the kiln from overheating and guarantees it’s operating correctly.
Most pottery kilns—especially the more modern ones—will automatically turn off if the control panel begins to overheat. Every three months, clean out and inspect the vent. Additionally, it depends on how frequently you use your kiln. Installing an exhaust system can help maintain temperature stability even more. It can also safeguard people’s health and encourage cleaner firings, which produce more vibrant glaze colours with fewer glaze faults.
Kiln Furniture Maintenance
Placing kiln shelf posts uniformly beneath the shelves throughout the kiln is crucial. It lessens the likelihood of warping during firings that entail high temperatures. Replace any shelves that begin to fracture immediately. Avoid taking the chance of a shelf breaking when firing and positioning the shelf directly onto the kiln’s bottom. It affects the firing process and can harm the fire brick.
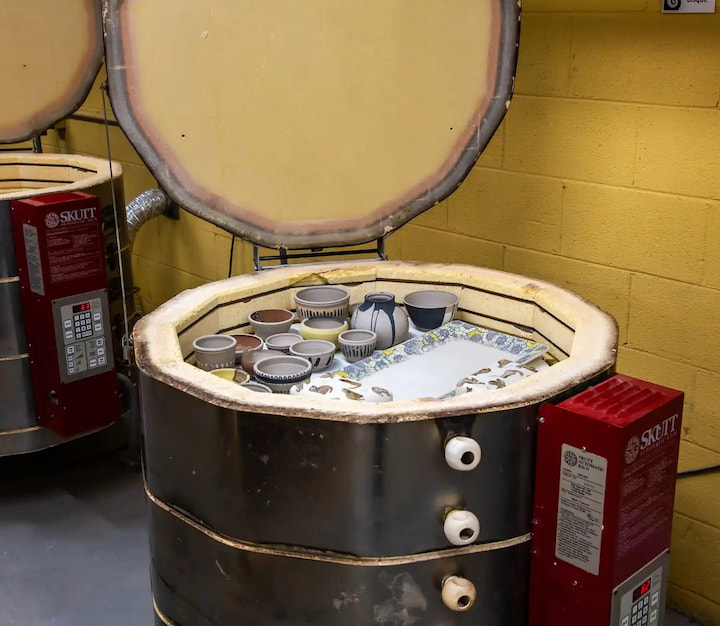
Kiln Wash
You can reduce the damage caused by dripping glaze by using kiln wash (also known as a batt) on the shelves. While it’s available as a ready-made option, purchasing the wash as a powder is the most affordable option and relatively simple to prepare. Only combine a small amount of the powder with water.
Most strive for a consistency that falls in between cream and whole milk. Next, apply two or three coats of paint to the upper portion of the kiln shelf. Only the upper side of the shelf requires kiln wash. Not the underside, not the side edges.
Certain manufacturers recommend scrubbing the kiln’s bottom using the specialised wash as well. While some don’t do anything like this, as they try not to tamper with the bricks too much, other potters will take this action. It’s crucial to prevent inadvertently getting the batt wash on your elements if you decide to perform this action. To achieve this, line the kiln’s sides with paper or cardboard before painting the base.