Important Things to Consider When Buying a Heat Sealer
Sealing your products properly is crucial for maintaining their functionality and extending their shelf life. A strong, reliable seal ensures that the contents are protected from environmental factors such as moisture, air, and contaminants. This is where a good heat sealer comes into play. Used widely in industrial laboratories and the packaging industry, heat sealers employ heat and pressure to join thermoplastic materials together, creating a durable seal.
Why Invest in a Good Heat Sealer?
To meet your sealing needs effectively, investing in a high-quality heat sealing machine is essential. Heat sealers are versatile tools used in various applications, including foil sealing, film media, plastic ports, heat seal connectors, and thermally activated adhesives. These machines often come equipped with advanced features, such as a PID controller for precise temperature control and a dwell timer that can be set for up to 99.9 seconds, allowing for accurate and consistent sealing.
One of the standout features of a good heat sealer is its ease of installation and minimal maintenance requirements. With a high heating capacity ranging from ambient temperature up to 250°C, and equipped with an advanced PID controller for effective temperature control, these machines ensure reliable performance. The auto-tuning function further enhances temperature accuracy, making them ideal for inspecting flexible packaging films for heat sealing quality. By using a heat seal tester, you can ensure your products remain unaffected by external temperature changes.
Important Buying Considerations
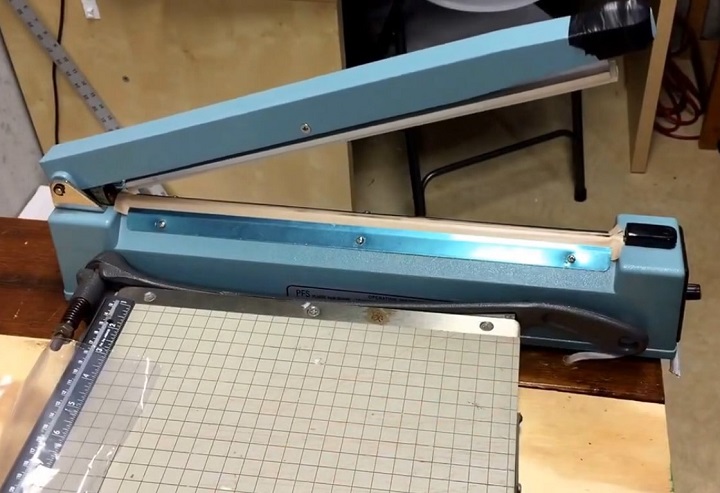
With a wide variety of heat sealers available on the market, finding the right one for your needs can be challenging. Here are some key factors to consider when shopping for a heat sealer:
Types of Heat Sealers
Impulse Sealers
Impulse sealers operate by first applying a brief pulse of energy to the sealing area and then quickly cooling it down. They do not require a warm-up time and only draw power when the sealing jaw is lowered. These sealers are suitable for materials that need a lower sealing temperature, such as polyethylene (PE) and polypropylene (PP).
Materials commonly used with impulse sealers include coated bags, Kel-F, Polyflex, Mylar, Tyvek, polythene, polyurethane, polyvinyl chloride, Pilofilm, polyvinyl alcohol, nylon, Saran, bubble packs, padded mailers, foil, and coated bags. Impulse sealers are energy-efficient, safe (as no components remain hot), and easy to use.
Direct Heat Sealers
Direct heat sealers, or constant heat sealers, maintain a consistent temperature in both sealing jaws. These sealers are ideal for thicker materials that require more heat penetration, such as coated aluminium foil, poly cello films, gusset bags, coated Kraft papers, waxed paper, cellophane, Mylar, coated PP, and other thicker materials. They consume electricity continuously when powered on, making them less energy-efficient than impulse sealers, but highly effective for robust sealing tasks.
Vacuum Sealers
Vacuum sealers remove air from the packaging before sealing, making them perfect for applications where preventing oxidation, spoilage, or corrosion is critical. For long-term storage, barrier bags are used as PE and PP bags are permeable. Vacuum sealers are essential for preserving the quality and longevity of perishable products.
Size
The size of the sealer should match the width of the material you need to seal. To ensure easier handling, it’s often recommended to choose a sealer that is at least one inch wider than the material. Sealers usually come with cutters that trim the material to a width slightly smaller than the arm width, providing a neat and secure seal.
Speed
Sealing speed is an important consideration, especially for high-volume operations.
Portable Sealers
Portable sealers are lightweight, versatile, and convenient, though their sizes are limited. They are the simplest and most affordable option, with manual operation requiring you to lower the sealing bar by hand. These models can handle about 6-20 packages per minute, with sizes ranging from 4″ to 40″.
Foot Sealers
Foot sealers offer faster operation compared to hand models. With a pedal-operated sealing bar, your hands are free to manage the packaging process. These options can handle about 8-20 packages per minute, with sizes ranging from 12″ to 35″.
Automatic Sealers
Automatic sealers are ideal for high-production environments, providing even faster sealing than foot sealers. These tabletop models feature dial-controlled sequence timers that automatically trigger the sealing jaws. They also have foot pedals for semi-automatic operation. Automatic sealers can handle about 20-50 packages per minute, with sizes ranging from 12″ to 47″.
Continuous Band Sealers
Continuous band sealers offer the fastest sealing process, with an infinite length capability. Bags are placed on a conveyor belt and fed through the sealer. These models can include features such as left or right feed, gas purging, a tilting seal head, vertical or horizontal seal head, and coding or imprinting options.
Width of Seal
The seal width is determined by the heating elements, typically made of nichrome or nickel-chromium. Most sealers allow for interchangeable use of round and flat heating elements. Round wires are used to cut and seal simultaneously, leaving no excess material above the seal. Flat wires come in various widths, including 2-3mm, 5mm, 8mm, and 10mm. Some feature dual heating elements for faster heat penetration, making them suitable for thicker materials.
By carefully considering the type, size, speed, and seal width of the heat sealer, you can ensure you choose the best machine for your specific needs. Investing in a quality heat sealer will provide reliable performance and extend the shelf life of your products, ensuring they remain in optimal condition.