Air Compressors 101: How to Choose the Right One for Your Needs
Inflating tyres, powering fridges and air-conditioners, driving air tools, pressure washing driveways, and spray painting walls or car panels are just a few of the everyday uses of air compressors. You’ll also see them in drilling applications in huge oil rigs, packaging and sealing food and beverages, and providing power in remote construction and mining sites.
This is just scraping the tip of the iceberg, and there are thousands of industries and everyday tasks where air compressors take centre stage. Of course, different types are meant for different applications, so choosing the right air compressor for the job goes without saying.
What are Air Compressors?
These are mechanical devices that convert atmospheric air into compressed and pressurised air that can then potentially be used for its stored kinetic energy. They do this in slightly different ways while using different power sources, meaning there are several types of compressors.
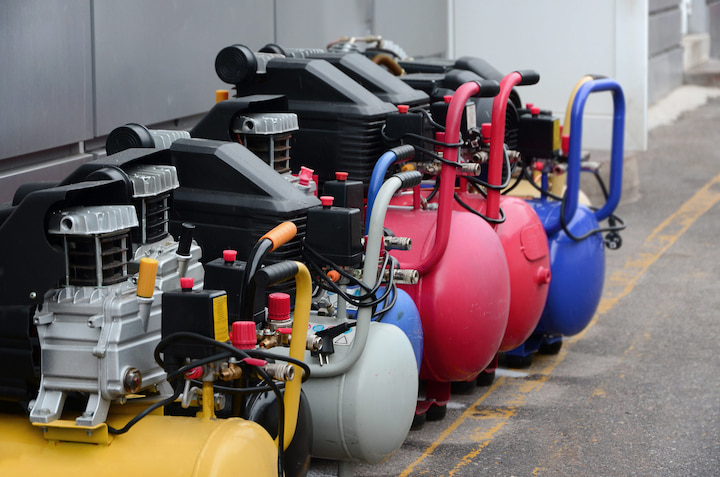
Most Common Types
Compressors are often categorised by how they compress and pressurise air. The two types in this respect are positive displacement and dynamic compressors. The first draws air into a compression chamber and mechanically reduces the volume of the chamber until a set pressure is reached. The compressed air is then discharged through a valve at the rated pressure. The most widespread variant here is piston or reciprocating compressors, and the ones you’ll see carpenters, mechanics, and construction workers using daily.
More complex industrial applications deploy rotary screw compressors that compress much larger volumes of air using two internal rotors or ‘screws’ turning in the opposite direction. The two types also differ in the power they produce, their overall dimensions, their ease of use and maintenance needs, and normally their price. Rotary compressors can be very expensive but are requisite installations in manufacturing and production facilities that rely on compressed air 24/7.
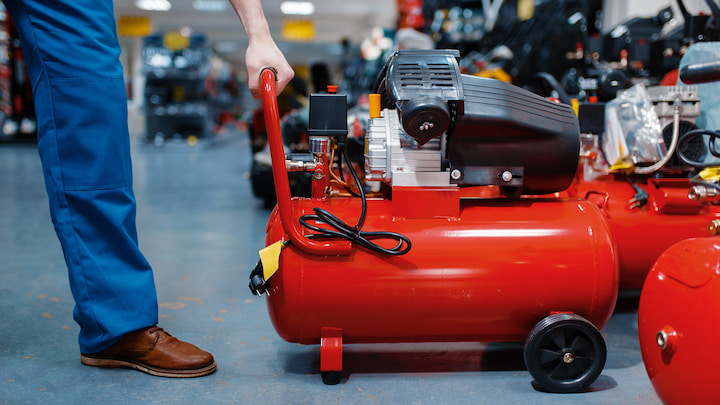
Dynamic compressors create power by forcing air inside with blades spinning thousands of times each minute, then restricting the space and pressurising the air. They’re often seen in car and aeroplane engines. Axial compressors are common in jet engines, while centrifugal types are a major feature of turbocharged cars as well as large chemical plants and steel production sites.
Benefits of Using Air Compressors
Air compressors are the preferred power source for multiple uses. This stems from a wide range of benefits:
- High power ratings – regardless of whether you need an air compressor to drive drills, angle grinders, sanders, framing guns, or other tools, or huge compressors in manufacturing or HVAC installations, all types provide high power when and where you need it.
- Efficiency – compressors can run on multiple power sources, such as diesel, petrol or electricity, but provide more power at much lower costs. This aids productivity and also reduces environmental effects.
- Flexibility – the device can be used to power several different tools, meaning you’ll only need one compressor at the worksite. Additionally, compressors may be the only power source in construction and other sites lacking a stable mains supply. Here portable compressors prove their worth.
- Quiet operation and low maintenance – A handful of features means compressors run at low noise levels, a prerequisite for many workplaces. Their robust build, and generally simple operation also mean low maintenance costs and reduced downtime.
- Safety – a compressor can be safely used in multiple conditions, including high temperatures. They also minimise the safety risks that come with electricity, such as electrocution.
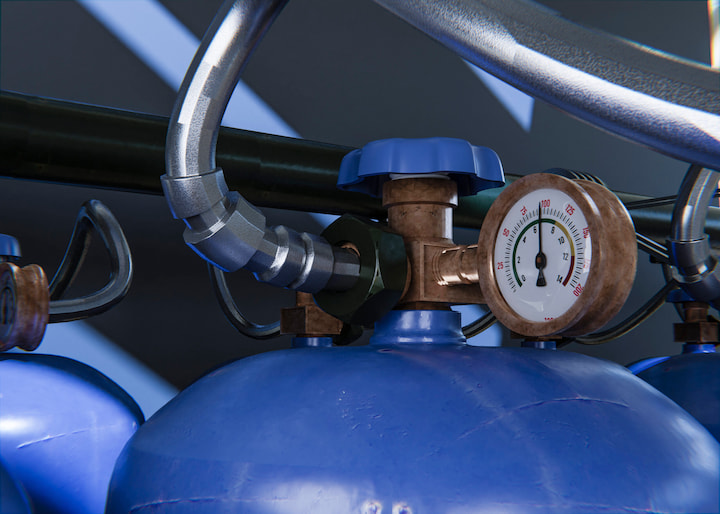
Choosing What’s Right for Your Needs
Several factors will determine the compressor that best suits your needs. Often these are interdependent. This includes airflow, air pressure, tank storage space, overall power ratings, how the compressor is powered and duty cycles. Build quality, easy maintenance, size, portability and silent operation are other things to consider before parting with your money.
Airflow
Airflow is measured in litres per minute (LPM) and relates to the volume of air the compressor can muster at a defined pressure. Higher numbers mean the compressor can consistently power even more demanding tools or equipment. As an illustration, smaller piston compressors can push out 100 LPM, or enough to power larger impact wrenches or hammer drills. Rotary screw compressors generate considerably higher airflow (up to 10 times more than competing reciprocating types) and can sustain this for longer periods.
Air Pressure
Air pressure is measured in pounds per square inch (PSI) and determines the force acting on a defined area, or put simply, the work that air can do. Compressors with a higher working pressure are at the same time more powerful and more efficient, so do more work with less fuel or electricity.
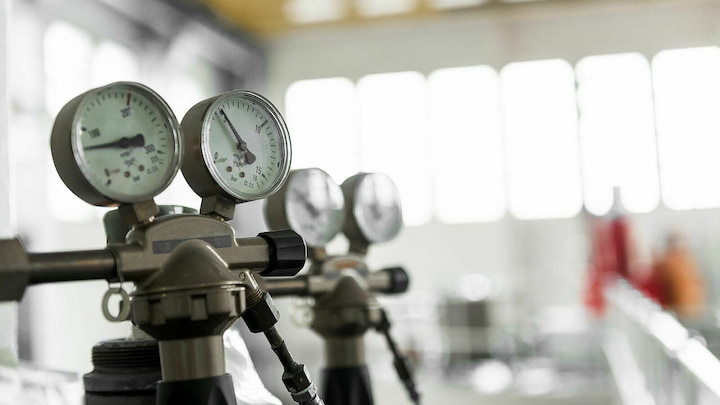
Tanks
To have compressed air ready, compressors use tanks. These are sized according to the airflow and pressure ratings. Some compressors have twin tanks and allow long work times. Tanks range from 20 litres in smaller piston compressors to over 300 litres in rotary screw variants.
Power Ratings and Power Source
Diesel, petrol or electricity are the main power sources for the majority of compressors. Portable units can be 12 or 24V battery-powered, or run on fuel, while larger and more powerful stationary rotary types use three-phase electricity.
With higher power on tap, compressors can reach the needed flow rates and pressure faster, and maintain these for longer periods. Smaller electric piston variants generate between 1 and 3hp, bigger diesel and petrol types average around 10hp, while screw compressors generate between 10 and 20hp.
Duty Cycles
If you rely on a piston compressor as your main power source, then look for longer duty cycles. This is the time a compressor can operate at a defined pressure, usually at 100PSI, and is determined by the unit’s power rating, efficiency and tank size. Duty cycles are stated as a percentage. Reciprocating compressors that have a 100% duty cycle won’t need to stop working to cycle in more air, so help with productivity and additionally endure lower wear.
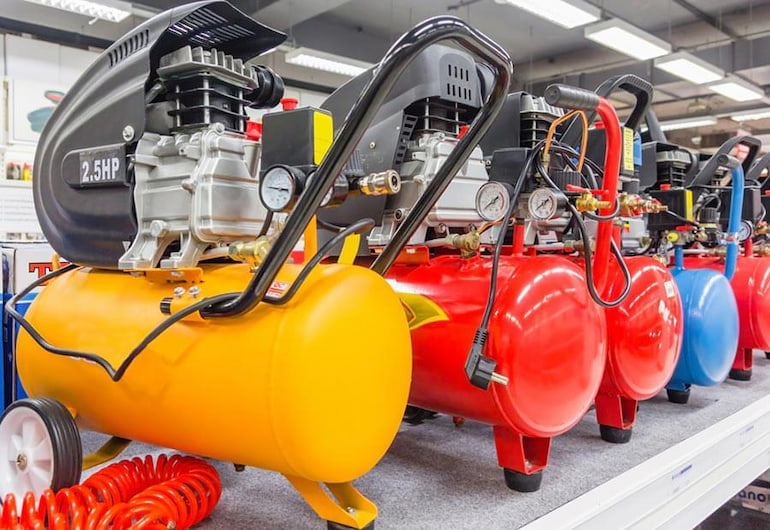
Other Considerations
Size and portability impact how and where compressors are used. Smaller, portable units running on DC power will be good for inflating tyres, or smaller tools but can fall short in more demanding tasks. Diesel or petrol units in medium sizes and weights are ideal for worksites without a nearby mains connection, and come either as wheeled options or have forklift pockets for simple manoeuvering. Screw types are stationary, rely on industrial power supply and often need more space to work safely.
Prices naturally vary by the build quality, features that up efficiency (belt or direct-drive motors, piston types etc.), whether they are oil or oil-free, and how loud they get when operating.
To get the right compressor, balance the overall airflow, pressure and power the unit makes, the capacity of tanks, rated duty cycles and features that work best in the environment you’ll be using it. Lastly, consider established brands and always shop from respected retailers.